The future of America's Rust Belt
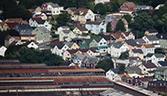
Millions of manufacturing jobs have gone in the former industrial heartlands of the US in the past few decades. In an effort to counteract this, state bodies are joining forces to attract FDI and ensure they can offer the skilled workforce demanded by investors. Natasha Turak reports.
More than 30 years ago, Bruce Springsteen epitomised the struggles of working-class Americans in his 1984 album Born in the USA.
Referencing the economic paradigm shifts that had rocked the industrial powerhouses of the Midwest, in the song My Hometown he sang: “Now Main Street’s whitewashed windows and vacant stores, seems like nobody wants to come down here no more. They’re closing down the textile mill across the railroad tracks, foreman says these jobs are going boys and they ain’t coming back.”
In 2016, that pain appears to be alive and well, manifested in the increasingly intense rhetoric against free trade and globalisation permeating the US election cycle. Presidential candidate Donald Trump has arguably been the most vocal of his peers in seizing on these frustrations, saying he would “gladly accept the mantle of anger” of disaffected voters.
Gloomy numbers
The statistics are grim: more than 5 million manufacturing jobs have been lost in the US since 2000. The term Rust Belt was coined to describe the economic decline across the region straddling the upper north-east US, the Great Lakes and the Midwest. Pennsylvania and Ohio, critical battleground states for the US election, saw a respective 35.1% and 30.3% drop in manufacturing jobs between 1994 and 2015 according to the US Bureau of Labor Statistics.
At the same time, paradoxically, output has increased. The US accounts for about 21% of the world’s manufacturing output, a figure that has remained consistent for the past 40 years. Statistics show US production has grown sixfold since 1944.
Gross output of US manufacturing, including value-added production, was $6200bn in 2015, or 36% of US GDP, according to a report by MarketWatch. And topping $1200bn in 2015, manufacturing comprised nearly 40% of total FDI stock in the US.
The disparity between employment and output can be explained by record gains in productivity aided by technology and advances in automation – today, factories produce twice what they did in 1984, but with one-third fewer workers.
A study by the Center for Business and Economic Research at Ball State University found that productivity growth “caused 85% of the job losses in manufacturing from 2000 to 2010, a period that saw 5.6 million factory jobs disappear. In that same period, trade accounted for a mere 13% of job losses.”
Automation bites
Thomas Grennes, professor of economics at North Carolina State University, wrote in 2013: “To the extent that increases in worker productivity were a result of technological innovation, jobs will not come back.” Automation, productivity increases, growing trade deficits and the shift towards a service-centric economy have changed the face of industry in the US and the jobs that come with it.
Yet in terms of foreign investment, manufacturing employment appears to be moving in a positive direction. Three in 10 manufacturing workers in key ‘swing’ states – Ohio, Pennsylvania, Florida and North Carolina – are supported by global investment, statistics from the Washington, DC-based Organization for International Investment (OfII) show.
In the past five years, Ohio and Pennsylvania’s FDI employment increased by 18% and 19%, respectively, while the states’ overall private sector employment increased by a respective 5% and 6%. In North Carolina, FDI employment jumped 31% in the same period compared with an overall state increase of 7%.
“The impact FDI has in terms of R&D dollars and increased exports, the training, the corporate social responsibility, [this] cannot be understated,” says Aaron Brickman, senior vice-president for strategy and development at OfII. “These are the jobs we need in the US and the jobs states are seeking.”
FDI jobs on average also pay 30% to 40% more than the state averages across these states. Foreign-headquartered companies now invest nearly $750bn in US manufacturing and employ more than 1.6 million people, according to the National Association of Manufacturers.
“You can’t talk about FDI without talking about manufacturing,” says Mr Brickman. “The growth of manufacturing jobs in the US through FDI far outpaces the growth of jobs in manufacturing as a whole, which has declined over time. FDI jobs in manufacturing have not seen the same decline.”
Skills needed
Increasingly, however, these jobs require more highly skilled workers. For the swathes of Americans left out of work, skills training is crucial. According to the 2015 Manufacturing Institute and Deloitte Skills Gap Study, 84% of manufacturing executives surveyed say there is a talent shortage in US manufacturing.
“The US is falling behind our major competitors in mathematics and science achievement, graduating significantly fewer engineers and experiencing a major skills gap for production employees,” said the National Association of Manufacturers in a 2012 report. “Action is needed to ensure the next generation is prepared to succeed in the manufacturing workforce.”
State agencies and economic development organisations (EDOs) are often viewed as holding some of the responsibility for developing local workforces to attract investment, and in the current economic climate this would appear to be more important than ever.
“The biggest drivers of where companies decide to locate is the strength of the workforce and the sites available for businesses,” says Will Bernstein, senior policy analyst at the Allegheny Conference on Community Development, which serves the Pittsburgh area and nine surrounding counties in Pennsylvania. “A major challenge is aligning the training with the needs of employers – it can be hard for the education system to keep up with the pace of technology change.”
Through its Regional Investors Council, comprising more than 300 private sector members, the Allegheny Conference develops programmes and funds for workforces, communities and site development.
“Foreign investment, at least in manufacturing, has often played a key role in improving training opportunities for American workers,” says Alan Berube, deputy director at the US-based Brookings Institute’s Metropolitan Policy Program. “This is particularly true for multinational firms headquartered in countries such as Germany, Switzerland and Austria, where there is a stronger tradition of programmes such as apprenticeships that prepare young people for careers. There are lots of examples of this in the south-east of the US and the Midwest, where foreign investment from those countries is strongest.”
EDOs and state agencies are well aware of the changes ahead. David Misner at the Pennsylvania Department of Community and Economic Development (PDCED) says: “A new economy means new industry, and the department works with employers to see what is needed to meet the challenge of training for emerging industries. Robotics, mechatronics and non-traditional apprenticeships are just a few of the newest innovations that require new ways of thinking about workforce development.”
Collaborative efforts
Mr Misner says that Pennsylvania's education department, universities and vocational training schools work in collaboration with industry to match their needs and help the unemployed get jobs. Similar to many EDOs’ initiatives across US states, the PDCED’s Workforce and Economic Development Network of Pennsylvania programme works with foreign and domestic companies, providing funds for a variety of training areas from welding to software engineering and advanced manufacturing technology.
“Since the inception of the programme in 1999 and through 2014 and 2015, the programme has funded training for more than 1.1 million Pennsylvania employees in almost 18,000 different companies,” says Mr Misner. “The most recent annual report for fiscal year 2014-15 shows an investment in training of more than $8.2m used to train 39,497 Pennsylvania employees.”
The future of manufacturing is highly advanced and technological, but critically, it is lean. States’ ability to attract FDI is pivotal to supporting this development and growth, but the numbers suggest that inevitably not everyone will end up with the employment and security they had in the past.

Global greenfield investment trends
Crossborder investment monitor
|
fDi Markets is the only online database tracking crossborder greenfield investment covering all sectors and countries worldwide. It provides real-time monitoring of investment projects, capital investment and job creation with powerful tools to track and profile companies investing overseas.
Corporate location benchmarking tool
fDi Benchmark is the only online tool to benchmark the competitiveness of countries and cities in over 50 sectors. Its comprehensive location data series covers the main cost and quality competitiveness indicators for over 300 locations around the world.
Research report
fDi Intelligence provides customised reports and data research which deliver vital business intelligence to corporations, investment promotion agencies, economic development organisations, consulting firms and research institutions.
Find out more.