3D printing edges into the supply chain
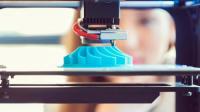
Its champions say 3D printing will cut export regulations, slash transportation and distribution costs and simplify supply chains, while transforming the manufacturing landscape. But will it be all they claim?
Last year, sports apparel manufacturer Adidas released its much-hyped 3D-printed shoes, the Futurecraft 4D sneakers. To be clear, the shoe was not made entirely by additive manufacturing, as 3D printing is also called, but rather just the midsole.
The sportswear giant had been printing midsoles in its 3D print prototypes but, until recently, was unable to mass-produce them, according to Carbon, the start-up that Adidas partnered to make the shoe. New advances in technology have changed this, however, and Adidas now hopes that within a few years it could be printing up to five million shoe parts.
There are many other examples of the game-changing use of 3D printing in manufacturing, but the case of Adidas has struck a chord in the site selection community. It has become clear that the rapidly improving 3D printing technology, coupled with other hi-tech trends, could conceivably usher in an era of truly distributed manufacturing, with smaller factories located closer to urban areas and substantially lower transport and storage costs.
Major benefits
For multinational companies, the benefits appeared to be even greater. Because 3D printing is based on the export of data, such companies could avoid onerous export regulations or even bans, while transportation and distribution costs could be slashed and a complex, multiple-touch supply chain simplified.
Many industries, especially auto manufacturing, have been aware of these advantages for some time. “Ford and Tesla don’t want to talk about additives because it is key to the future of auto manufacturing,” says Ryan Martin, principal analyst at ABI Research’s Industrial Solution. “It will be a competitive differentiator and a huge advantage. It can cut the current multi-month design cycle down to weeks, producing huge savings.”
That said, the vision is still some distance away from becoming a reality. Today’s experts cannot imagine how 3D printing could make traditional factories and manufacturing processes obsolete. What is more, an academic study suggests the benefits of additive manufacturing may not viable for all manufacturing in certain scenarios.
Changing scenario
Still, the technology is evolving faster than expected and this view of the industry could well change. Already, it is clear that 3D printing of parts and products is on an upswing. ABI Research estimates there will be $11.5bn-worth of products and parts manufacturedthis way in 2019, says Mr Martin. By 2030, the firm estimates that globally, $360bn-worth of parts and products will be manufactured using this technology. “Increasingly, manufacturers are showing real signs of 3D printing adoption,” he says.
Last year, for example, GKN Powder Metallurgy, a global company headquartered in Radevormwald, Germany, announced a 3D metal printing partnership in which it would use HP’s Metal Jet additive technology to produce functional metal parts for auto and industrial leaders, including Volkswagen and Wilo. “With these ever-expanding additive technologies, the parts you can build are getting larger, ranging from the size of a golf ball to the size of a beach ball,” Mr Martin says. “It is, clearly, not a viable technology yet for producing whole products, but it is seen as an attraction option for producing parts, especially intricate ones.”
The technology will progress to the point that the location of factories will no longer be as important as they are now, says Avi Reichental, CEO of Techniplas Digital, a supplier to auto manufacturers such as BMW, Daimler, Ford and Fiat.
“3D is coming of age with a variety of converging capabilities: speed, greater material availability, more intelligent design,” he says. “Put it all together and one can easily see that in five to 10 years, who makes cars and how they are being made will be more application and market-specific as opposed to the stronghold big automakers have on the industry now.”
Couple this with other technologies that are rapidly developing, such as autonomous vehicles, Mr Reichental adds, and new, local manufacturing opportunities will emerge because the barriers to entry will be so much lower. “Manufacturers can avoid the trade wars as well because they are teleporting designs without the accompanying freight,” he says.
Specific use
It is important to note that 3D manufacturing cannot cover the entire manufacturing spectrum, says Alkaios Bournias Varotsis, technical marketing engineer at 3D Hubs in Amsterdam. To begin with, most 3D parts still need post-processing, he says. There is also a cultural element for companies to address, especially smaller manufacturers: sourcing materials can be expensive for these firms, which cannot afford their own sourcing department, he adds. Bigger companies are also more likely to have familiarity with the technology.
In response, some of these smaller suppliers are taking an incremental approach to 3D, according to Mr Martin. “For example, a company can begin trialling [3D] with tools on traditional equipment and spare parts, allowing its employees to get familiar with the software. Once they become used to using it internally, the manufacturer can move to designing for production.” For these companies, a gradual approach is better, especially as the industry moves closer to the ideal world of smaller, localised factories with lower storage and transportation costs.
But what if this ideal 3D-based manufacturing world turns out to be unrealistic, despite all the new investment and advances in technology?
Non-critical parts
A new study by researchers from Carnegie Mellon University’s department of engineering and public policy and the University of Lisbon investigated how additive manufacturing could contribute to distributed manufacturing. They examined whether it would disrupt the current central model, specifically in the context of spare parts for the aviation industry, where being able to print parts quickly rather than stockpiling them would be attractive.
“Our results suggest that 3D printing may not be as conducive to distributed manufacturing as some might hope,” says Parth Vaishnav, an assistant research professor at Carnegie Mellon. While decentralised 3D printing could reduce the need to carry inventory, the researchers say, the very expensive machines sometimes needed to process parts after they have been 3D printed may still favour centralised manufacturing. The team concludes that decentralising manufacturing would make economic sense for non-critical spare parts with combined annual production volumes in the tens of thousands.
While this may seem disappointing to 3D printing advocates now, it is important to remember that even a few years ago the scenario of production volumes in the tens of thousands was seen as unrealistic; 3D is rapidly evolving and numerous industries are waiting to see what shape it will assume.

Global greenfield investment trends
Crossborder investment monitor
|
fDi Markets is the only online database tracking crossborder greenfield investment covering all sectors and countries worldwide. It provides real-time monitoring of investment projects, capital investment and job creation with powerful tools to track and profile companies investing overseas.
Corporate location benchmarking tool
fDi Benchmark is the only online tool to benchmark the competitiveness of countries and cities in over 50 sectors. Its comprehensive location data series covers the main cost and quality competitiveness indicators for over 300 locations around the world.
Research report
fDi Intelligence provides customised reports and data research which deliver vital business intelligence to corporations, investment promotion agencies, economic development organisations, consulting firms and research institutions.
Find out more.